Technology Puts Muscle into Saving Time and Money on Construction
--
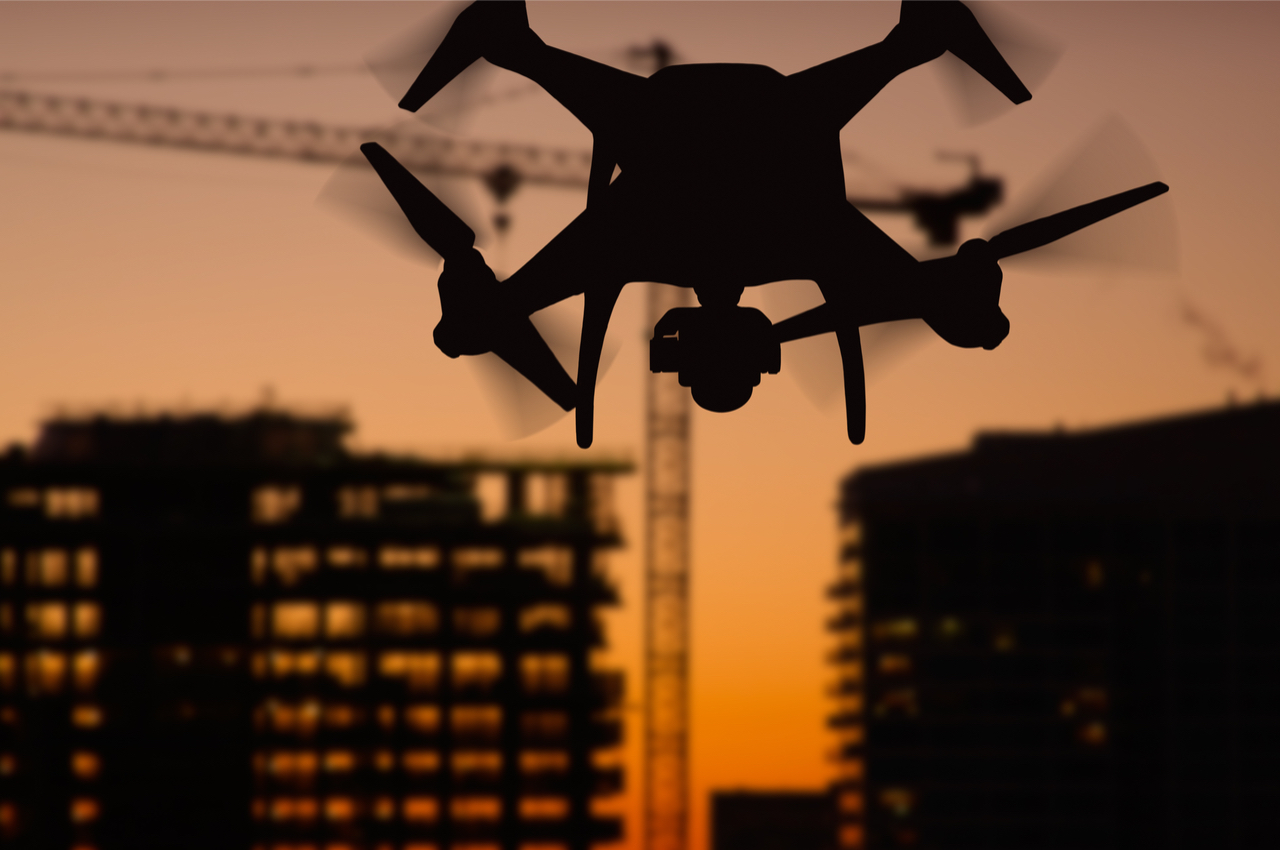
Ben Bruns of the Weitz Co. says that in some ways the construction industry was more efficient before World War II. Erecting buildings just didn’t take so long.
At a recent student housing conference, the company’s national development director pointed to the Empire State Building as an example.
Built in 1931, the wondrous tower stretched high above New York City and went up in 13 months, at a cost of $41 million (about $550 million today). When the last brick was set, the 1,250-foot-tall, 120-story art deco masterpiece was declared the tallest structure in the world.
It remains a construction marvel, ranking in 2017 as the fifth-tallest completed skyscraper in the U.S.
A backstory to its glory is that, despite 15 revisions from the original design as a 50-story building, only 36 pages of drawings were needed to guide workers. The original plans took two weeks to assemble, a far cry from the months of paperwork and planning that go into commercial buildings nowadays.
In comparison, Bruns says, a paltry $55 million project today (that’s $3.5 million in 1931 money) requires a 100-page contract, most of which is devoted to payroll. Permitting and final paperwork typically take longer than the time required to construct the Empire State.
Conditions were different long ago, but the one constant is that skilled labor comes at a premium. Construction is very labor intensive — and dangerous. (More than 3,500 workers were needed to build the Empire State Building, and 42 reportedly died in the process.)
Nearly 90 years later, commercial and residential construction is plagued by excessive underwriting, labor shortages and pricy materials. Projects are more difficult to build just because of intricate designs that require a greater level of workmanship, lumber and steel so buildings stand out from the crowd.
Land in urban areas is sparse and costly. Developers are often left making the best of an imperfect lot, which requires extra time to survey and plan, plus more money.
The devil is in the details.
“Pay applications can be up to 60 pages of a contract,” Bruns told student housing leaders at the annual Interface Student Housing Conference in Austin this spring. “And we wonder how we get subcontractors paid in a timely fashion so they want to come do our jobs. We have to loosen some of the underwriting associated with it.”
But it’s not all bad. Technology is helping offset time and sky-high costs in today’s building processes, bureaucracy notwithstanding. It may not be the complete salvation of the modern-day building, but Bruns and the Weitz Co. see it easing some of the pain.
New technology, pre-manufacturing maximizing productivity
The industry is embarking on fresh techniques that require less brute strength and more technical power.
While automation and pre-manufacturing are already in the pipeline, Bruns and Weitz — one of the U.S.’s oldest construction firms specializing in commercial, industrial and heavy industrial projects — believe that construction will continue conforming to the latest advances as developers seek to build projects on time and under budget.
The company is using robots and drones to maximize productivity on job sites and help planners think through construction processes before the first load of lumber is delivered.
A few years ago in Omaha, NE, robots laid out a project and saved $100,000 in setup costs. On another project, they helped determine the precise amount of rebar (30,000 pieces) needed for concrete work on a building, and did so to near perfection. Only three of the pieces delivered to the site didn’t fit, a 0.0001 percent spoilage rate.
Better planning through technology was a big reason the 3,400-bed Park West student housing project at Texas A&M University in College Station, Texas, finished a week ahead of schedule.
“We took all the pre-development risk out of it,” Bruns said. “We funded all the schematic design — $1.8 million worth — for the opportunity to be involved in this project and get an above-market feel when all was said and done. It turned out to be a great project, a truly monumental accomplishment.”
Modular building reducing time at the job site
At a factory in Cincinnati, modular bathrooms were built and shipped to a flagship hotel project in Des Moines, Iowa. Bruns said the decision to pre-fabricate saved “17 weeks of chaos on the job site.”
Cranes hoisted finished modules, complete with tile and grout, onto the flat surface of the structure with ease. Because of their design, the bathrooms fit snugly against the surface of the rest of the apartment, with no transition from the carpet to the bathroom floor.
The modules were made of strong, lightweight composite material and metal studs so they could be shipped safely and minimize spoilage. All were installed about two weeks sooner than if crews had built them onsite.
Building the bathrooms in a factory offered some subtle assembly efficiencies that workers couldn’t gain otherwise, like applying thinner grout lines when setting tile.
“The grout joints on the tile are half the size of a normal installation,” Bruns said. “That means it doesn’t take as much work to clean it. Quality improves. The schedule was dramatically impacted.”
Overall, the company cut costs 7.5 percent.
The Weitz Co. also is leveraging technical know-how to stay on top of jobs, from planning to the final coat of paint. Drones are being used to better assess job sites before work starts and inspect structures as they are being built and after completion. The technology allows inspectors to see parts of high-rises that would normally be too dangerous for workers to access unless they used heavy equipment.
“We’re using drones to help us understand how productive we are, to see places we couldn’t see before,” Bruns said. “We’re seeing what the detail looks like way up high on new projects, those brand new student housing projects that everybody’s excited about.”
Along the way, end-of-construction punch lists are being redefined. In the past, nobody had a list that included scrutinizing a high-rise building’s façade well beyond the first few floors with as much specificity as possible today, Bruns said.
Pre-manufacturing could help ease labor issues
Bruns said building some components in advance could solve a chunk of the construction industry’s manpower issues, although some believe it’s not a perfect process. Among the reasons are that modules could be assembled incorrectly or take too long to build offsite or be damaged in shipment.
One architect at the conference said mold was found in some modules that sat outside too long at the site before being installed in one high-rise. The problem put the project behind schedule.
Others think the old-school way of assembling buildings is just faster and does not compromise control at the job site.
But Bruns said the industry may have to rely on pre-fabrication like it or not, especially if labor shortages persist.
It’s no secret that fewer workers are choosing construction as a career. Coupled with rising retirements, an already depleted labor force is just getting thinner.
“My prediction is that there’s going to be no choice,” Bruns said. “Manpower is going to continue to be scarce while the demand is going to continue to be there. The trades people are retiring at a rate that is absolutely alarming. Finding a mason right now in this country is a real challenge; in fact, we’re considering multiple masons on just about every project of scale because if somebody stumbles you have to be there to pick it up.”
Technology creating greater transparency in construction
The true impact of how technology is improving construction ultimately is in the bottom line and keeping it in check while minimizing cost overruns. Honing in on labor issues and on precise processes not impacted as much by spoilage and waste offers better transparency in pricing.
Bruns says the Weitz Co. already has greater pricing transparency and that this will become the norm with all construction companies when building commercial and residential establishments. Sort of like buying an everyday item off the grocer’s shelf.
“You know what it costs to buy, you know you like it and you know it does the job,” he said. “In the future, buying our services will be much more straightforward.”
To learn more about improving construction in multifamily, check out: A Job Costing Solution to Improve Multifamily Construction.